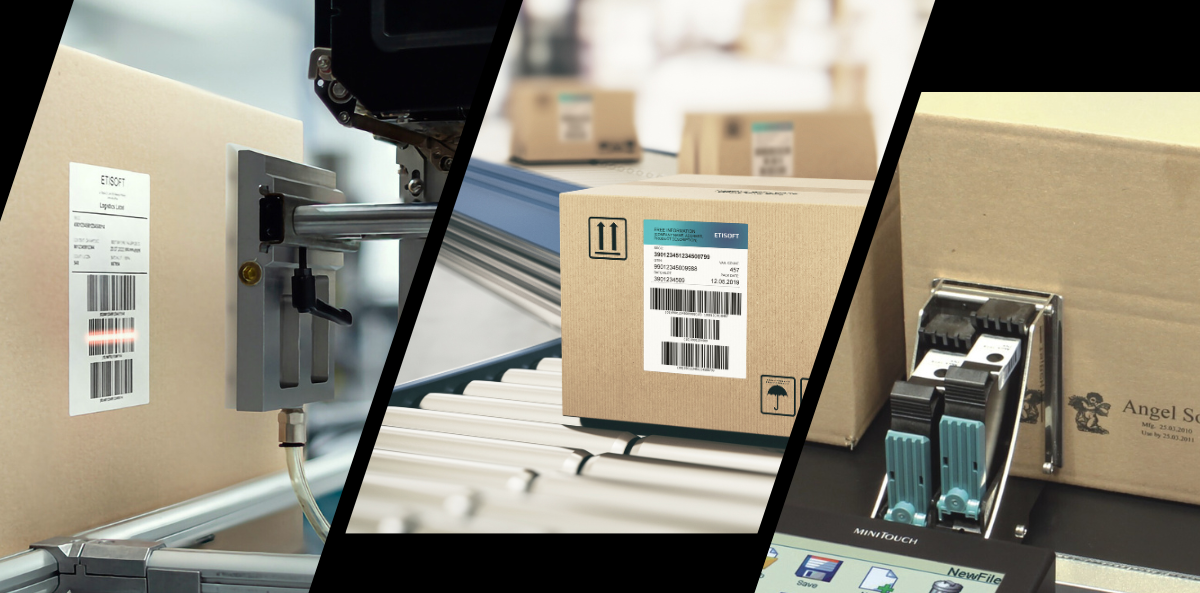
Automation of marking on production lines
Automation of processes in industry is one of the most important areas of improving the efficiency of enterprises. In particular, this applies to the automation of product marking, which allows for increased precision, speed and elimination of human errors. Modern technologies such as inkjet printing, laser marking and automatic labelling have become an indispensable part of production processes in many industries.
Benefits of automating your marking processes
Increasing market demands related to efficiency and effectiveness have forced manufacturers to implement automatic identification systems. Standardization of markings, barcodes, and RFID systems have become the backbone of the supply chain.
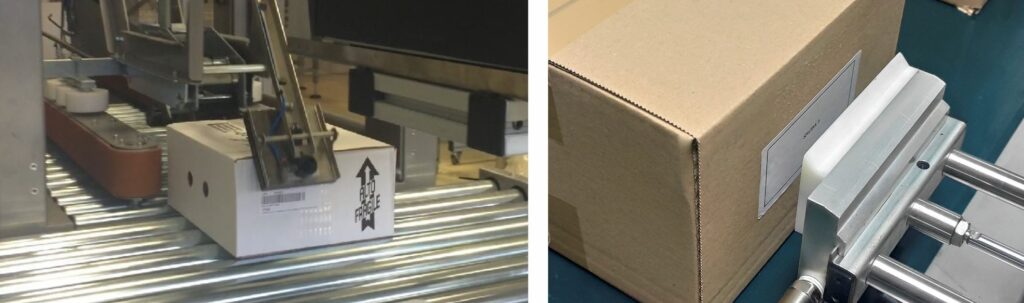
Automated marking has many advantages. The most important are:
- speed – automatic marking systems allow you to mark thousands of products in a short time, which increases the efficiency of production lines,
- precision – the use of advanced technologies makes the marking extremely accurate,
- elimination of human errors – automatic systems reduce the risk of errors associated with manual application of markings, which translates into higher quality of the final product,
- Increase in logistics efficiency – the flow of products through the supply chain becomes faster and more transparent. Standardization of logistics markings makes it easier to track shipping units and reduces the risk of delays and mistakes in deliveries,
- compliance with standards and regulations – automated marking systems help companies meet legal requirements and industry standards,
What is marking in industry and logistics?
In manufacturing processes, marking involves the assignment of identification numbers, symbols, and serial numbers that help with production tracking, quality control, and process management. Marking plays a key role in ensuring proper organization and efficiency of production.
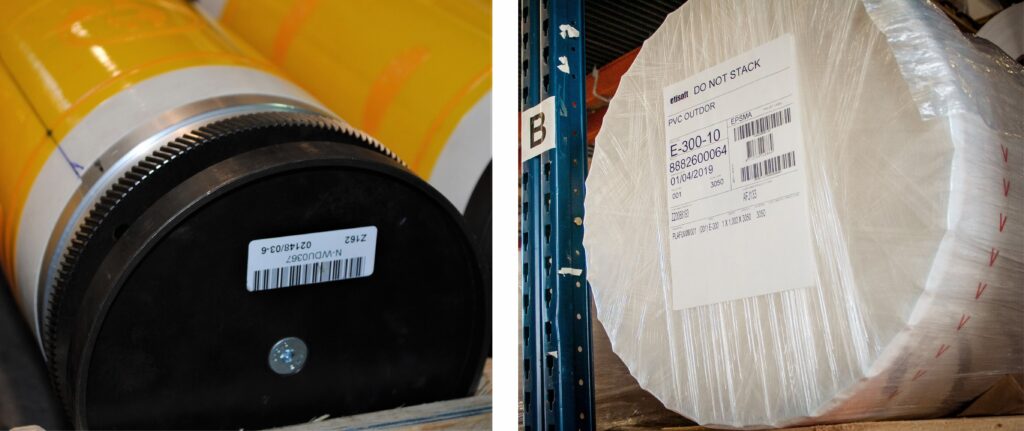
The following are subject to marking:
- Raw materials and materials used in production – are marked for the purposes of tracking throughout the production process, identification of origin, production date or expiry date,
- production elements – subassemblies, parts and components that require identification at further stages of assembly are marked with barcode labels or RFID tags
- finished goods – products marked with information such as batch number, production date, user manuals, country of origin, as well as quality information (e.g. certificates, test results).
- unit and collective packaging – labels are affixed to the packages with information about the contents, expiry date, storage requirements,
- shipping units – these are batches of products intended for shipment marked with the GS1 logistic label.
How to improve the process of printing and applying labels in the warehouse?
What are the marking technologies?
There are various product marking technologies available on the market, depending on the type of product and the specifics of the production process. The most commonly used marking methods include laser engraving, inkjet printing directly on production or on the box, barcode and 2D code labels and RFID tags.
- Inkjet printing directly on the product
Inkjet printing is an inkjet printing technology that allows you to apply a production and expiration date, serial number, barcode directly onto the surface of a product or cardboard box. Inkjet printing is fast, flexible, and suitable for a range of materials, including paper, plastic, and metal. Direct printing systems are installed on production lines in the food and cosmetics industry.
- Laser Marking – 2D Codes
Laser marking is characterized by high durability and precision. This method is especially popular for 2D codes such as QR or Data Matrix. It has gained particular importance in the heavy industry, automotive and electronics sectors. Marking is carried out by precise firing of the material. The laser is directed at the surface, creating microscopic depressions or changing the structure of the outer layer. The result is a contrasting and durable 2D code that is readable even after years of use and resistant to external influences. Laser technology enables marking on metals, plastics, ceramics or composite materials.
- Label printing and applicator systems
Print and Apply systems are used on production lines to print variable information on labels and then to stick them on the product or its packaging. The systems consist of a printing module based on thermal transfer technology and an automatic label applicator. The printing modules are adapted to the printing of texts, numberers, product weights, barcodes and 2D codes as well as to the encoding of RFID tags. The devices can be easily integrated with higher-level systems for managing label printouts. They are characterized by high performance, reliability and the ability to work 24/7.
Marking products with labels
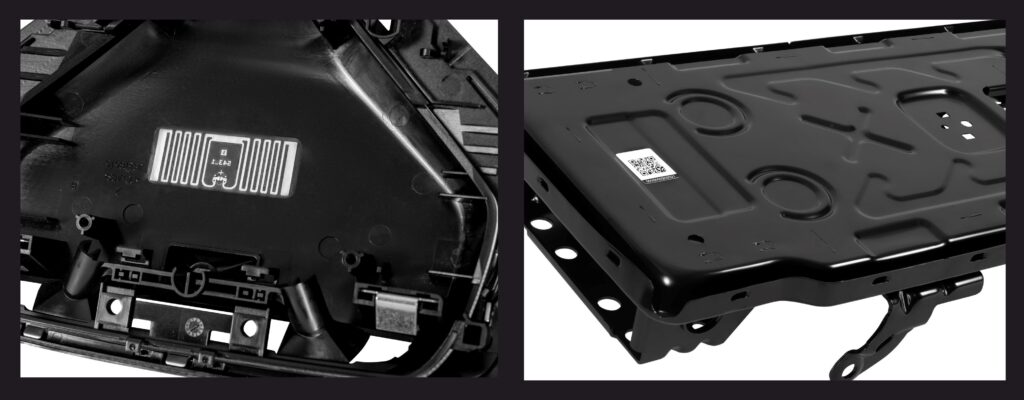
- barcode labels – this is a classic solution for product identification, containing a barcode or a two-dimensional 2D code. With these labels, it is possible to quickly and accurately scan data with scanners, which streamlines warehouse, inventory and logistics processes. Barcode labels are widely used, and their main advantage is the ease of implementation and low production cost.
- RFID labels – contain chips that enable remote reading of information using radio waves. An RFID label contains a small chip and an antenna that allows information to be sent to an RFID reader, allowing the data to be read remotely without the need for physical contact with the label. In addition, it is possible to read multiple tags at the same time. RFID tags are used where fast tracking and management of a large number of products is required, for example, in logistics, manufacturing, trade.
How to automate the printing and labelling process? Read on!
Automatic verification – vision systems and smart cameras
Verification of the quality of the marking is as important as the process of applying the markings itself. Detecting an error immediately after printing or applying a label allows for quick elimination of a defectively marked element, without incurring the costs of returns and complaints. Modern vision systems, including code verifiers, sensors and smart cameras, enable:
- control of the correctness of the printout – checking all elements printed on the label, correctness of data and verification of the color of the print,
- verification of barcodes and 2D codes – checking the correctness of the printed code in terms of legibility and compliance with standards,
- control of the correctness of label application – ensuring that the label has been correctly placed on the product.
Find out how to automate quality processes based on vision processes!
Automating coding on production lines is an investment that can increase efficiency, reduce costs and improve product quality. Etisoft specializes in providing innovative solutions in the field of automatic identification, automation of product marking and vision systems for verification of prints. The company provides professional technical support, software, maintenance services and consumables. It offers a wide range of product marking solutions, including adhesive labels, adhesive-free tags, and RFID labels.
By choosing Etisoft, you gain access to professional solutions that support production and logistics operations, as well as increase the quality and efficiency of processes.