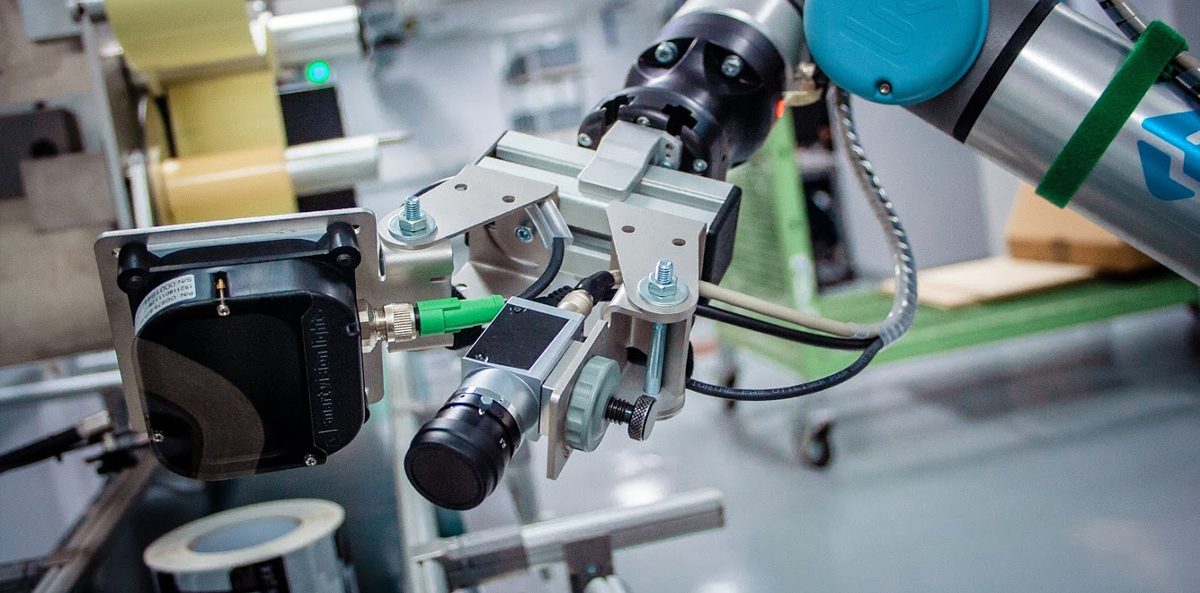
Automation of quality processes based on vision systems
Customer requirements regarding parameters of the purchased products are getting higher and higher, therefore manufacturers are putting increasing emphasis on quality control. However, the fact is that 100% quality control is a value which cannot be achieved even with the most engaged and meticulous employee. With a view to increase sales figures and while taking care of customer satisfaction and safety of the process, the assessment at a guess should be discarded and replaced with modern and precise solutions. Quality control vision systems and quality control automation are already present in many branches of industry, ranging from simple inspection tasks to complex and sophisticated requirements.
Vision system – challenges
Functionality, quality, design, many language versions, delivery dates… Regardless of the type of product, customer expectations are constantly growing. New trends shaped by both consumers and companies also influence how many of the objects and devices which surround us are produced. Shorter and shorter production batches, personalisation, increasing product turnover and shorter assembly line takt times are all challenges which many production plants have to face. Henry Ford’s motto of 1914,
“Any customer can have a car painted any colour that he wants so long as it is black,”
became obsolete a long time ago. The world has sped up and is not going to slow down.
Quality processes today
Wiele przedsiębiorstw w różnych obszarach swojej działalności wciąż realizuje kontrolę jakościową poprzez:
Many companies in different areas of their business still carry out quality control by
- choosing individual samples from the whole production batch (these are hundreds, thousands, sometimes millions of products) and carrying out manual measurements in the laboratory by qualified personnel with the aid of specialised equipment and software,
- an assessment made by a person, which, due to its nature, is subjective and dependent on the person, degree of fatigue, time of the day and is not repeatable. What is more, it is limited to the natural capabilities of sight, which make it impossible to meet the requirements of design/quality documentation (humans are not able to tell the difference between 0.5 and 0.8 mm, and definitely not in a repeatable and efficient way).
Moreover, the task is not made easier by
- production volume and short production takt time, and thus the speed at which production is carried out, which frequently makes human verification impossible (e.g., Etisoft produces labels at an average speed of 100 m/min. on some machines),
- the already mentioned variety of products – it is difficult for a human to remember the exact specifications of hundreds of types of products that are to be verified, especially when frequent changes in personnel are considered.
Automation of quality processes based on vision systems
Automation enables companies to implement repeatable processes (among many other advantages) and to become independent from those aspects in which a human does not perform well.
The same concerns vision systems. The algorithms implemented through the selection of appropriate cameras, lighting, essential equipment, and structures, and created by experienced specialists, will make it possible to take quality processes to a new level.
Inspection of each component or product, repeatability and reliability of the measurement, the inspection results connected with the requirements specified in the documentation – these are obvious advantages.
While considering process automation, you can also go one step further and thanks to additional integration increase process awareness and address the growing diversity on production lines.
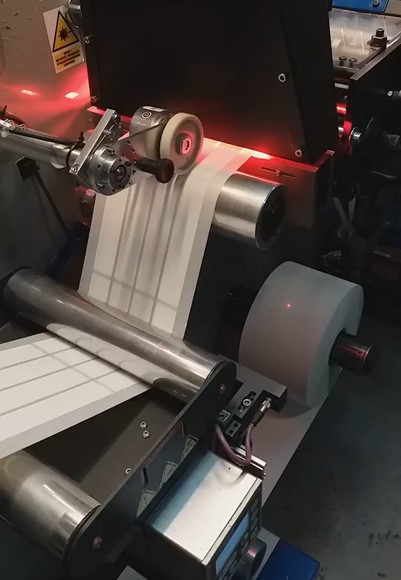
The first step is to identify the product model/variant to be inspected. It can be obtained by reading the ID number on the label, integrating with RFiD or the customer’s IT system, or entrusting the vision system with this task as well. In this manner, all the data generated during the inspection stage are placed in time and linked to a specific number which identifies the product. Thanks to that we can collect, process, and analyse large sets of data (statistical, time-based, per shift, per product, etc. analysis). Such data will be certainly valuable from the perspective of traceability or quality systems.
The next step, knowing the ‘identity’ of the product, is to integrate with the customer’s IT systems that contain information about BOM or technology of manufacturing the product in question, i.e., the systems on the basis of which the company produces its goods. Such systems constitute a valuable source of current data for process automation. They make it possible to determine, for example, the presence or type of the inspection object (variety, variation) and carry out the changeover of the system in an automatic way. An intermediate solution is to implement an additional configurator which can be operated manually or be a hybrid system (it can draw on both approaches).
The above-mentioned modules enable the operator to be relieved of plenty of duties and activities, thus increasing their productivity. Since the system carries out an inspection of each component/product, we can react in real time, which generates savings: operator time, machine time and raw material, which is frequently one of the main costs. This also makes it possible to detect critical situations (e.g., defects in the production batch of components) and draw conclusions regarding where to search for savings or improvements in the process.
Interested? Contact us!