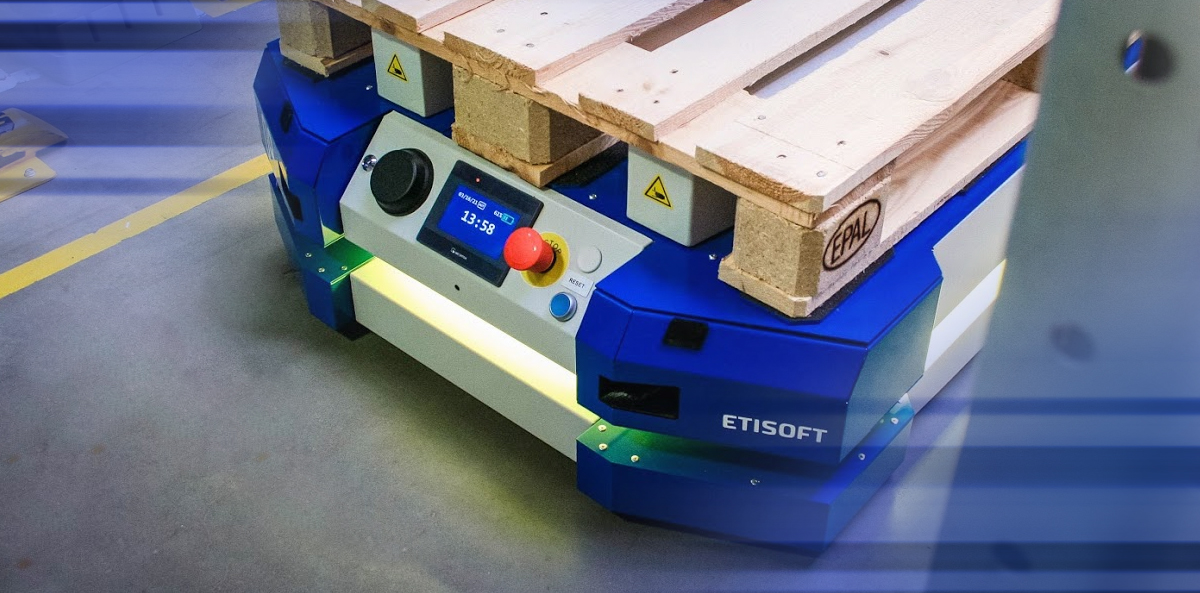
What is automated intralogistics? 4 components which an automated intralogistics system consists of. Part 1
Intralogistics is a special case of logistics where you have a brush with the flow of materials and information in a company. On the other hand, automation refers to the replacement of a human factor with equipment used to perform repetitive activities in the process.
When starting automation, you should divide intralogistics into parts and consider the possibility of integrating the machines, equipment, and software for handling intralogistics processes available on the market, or use the help of an experienced integrator, that is Etisoft Smart Solutions.
Intralogistics processes include:
- Receipt, issue, and transport of materials
- Order picking and sorting
- Inventory management
- Information flow management
- Warehouse management.
In addition to that, managing the safety of employees, for whom plant managers and OHS department are responsible, is an equally significant challenge. It is worth noting that automation increases work safety mainly because it is more predictable than the personnel. The equipment responsible for process automation, thanks to the application of latest technologies and tried and tested practices of ensuring safety, operates in the same way, regardless of the part of the day. Employees, on the contrary, become more and more distracted and less attentive over time.
What does an intralogistics system consist of in practice? Automated logistics – what do we mean by that? In the article below we will present 4 main components of the system.
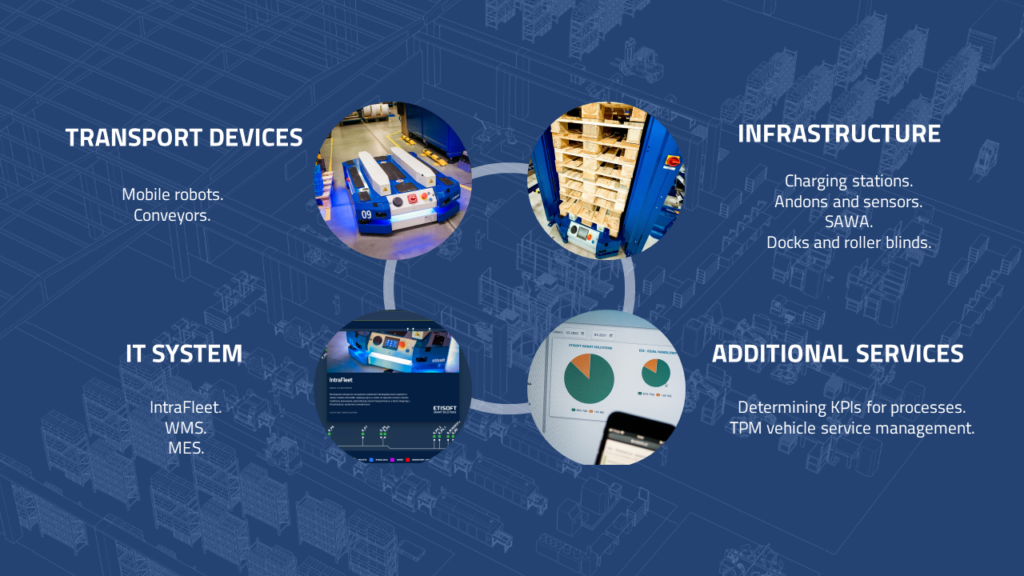
1. Transport equipment
The fundamental component of automated intralogistics is the equipment that performs the transport.
a. AGV/AMR.
Modern plants more and more often decide on autonomous vehicles, AGVs/AMRs of various types, which cooperate with people and adapt to the conditions of a dynamic production environment. Mobile robots for a particular company are selected depending on the type of a logistics carrier used and the working conditions. The most popular logistics carrier is a pallet (IntraBot Lift, IntraBot Fork). KLT containers (IntraBot Stand), baskets, wheeled carts, wagons (IntraBot Tow) and other logistics carriers can also be encountered.
Mobile robots can provide production with materials, tools, and parts. They can also pick up finished goods and transport semi-finished products to another stage of the technological process.
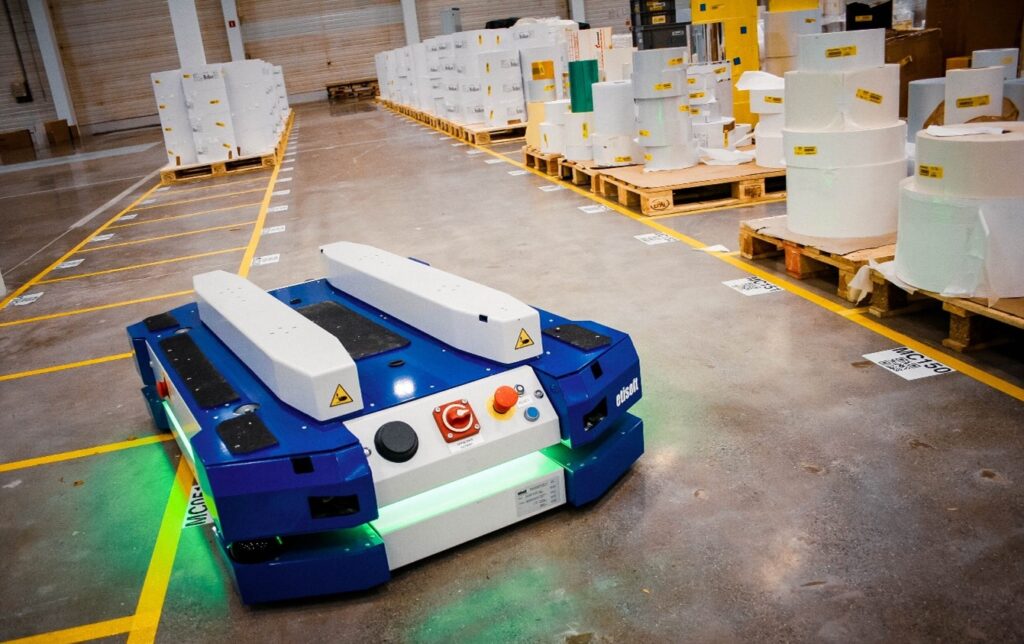
b. Conveyors
Conveyors are another solution. This is transport equipment statically installed in a production or warehouse hall. Conveyors can move goods by gravity without any additional load bearing force or using rollers or belts with electric drive systems. Compared to mobile robots this type of solution is usually cheaper to use, but not very flexible. In the case of implementation, the need for expansion or modification, the time, and finances to be spent are significant.
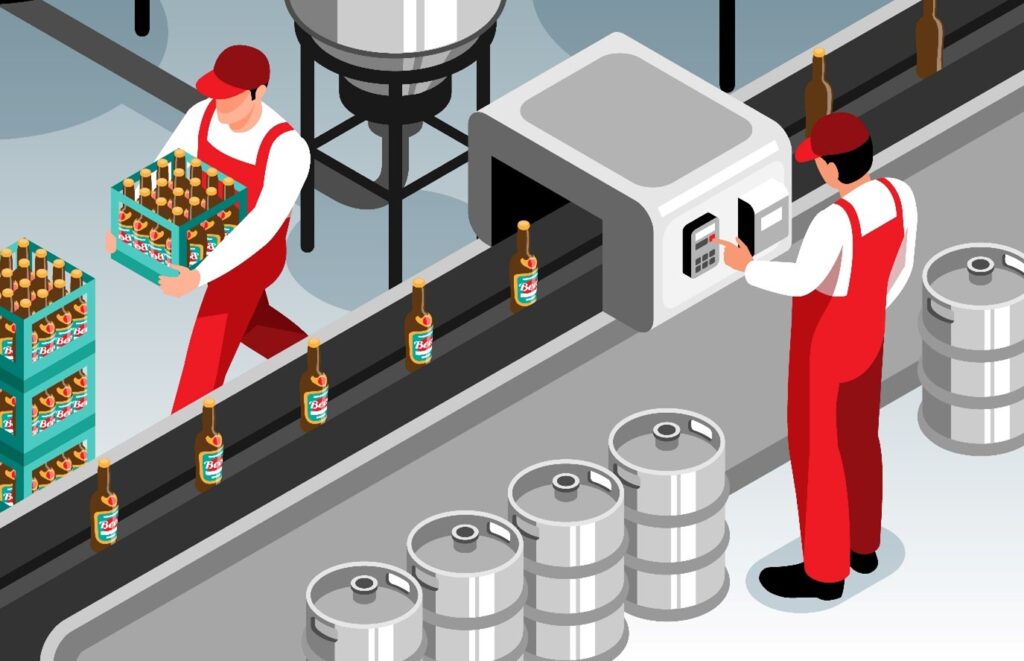
2. IT systems
The mechanical part of the intralogistics system comes into direct contact with physically moving components. The IT part, on the other hand, is responsible for the flow of information in the plant. Plant digitization, traceability, algorithms, and transportation mission triggers are all software issues which give shape and form to the intralogistics system.
a. Mobile robot fleet manager
The application for AGV/AMR management is an inherent part of the system that includes mobile robots (e.g., IntraFleet), since it is responsible for managing the movement of the robots. It includes, among other things, building a transport mission plan and analyzing continuously the mission path of each AGV/AMR. The application makes it possible to continually control and optimize the movement of the robots in space. It reduces the risk of transport process stoppages and congestion to an absolute minimum. The robot manager can be considered as part of the MFC (Material Flow Control) system.
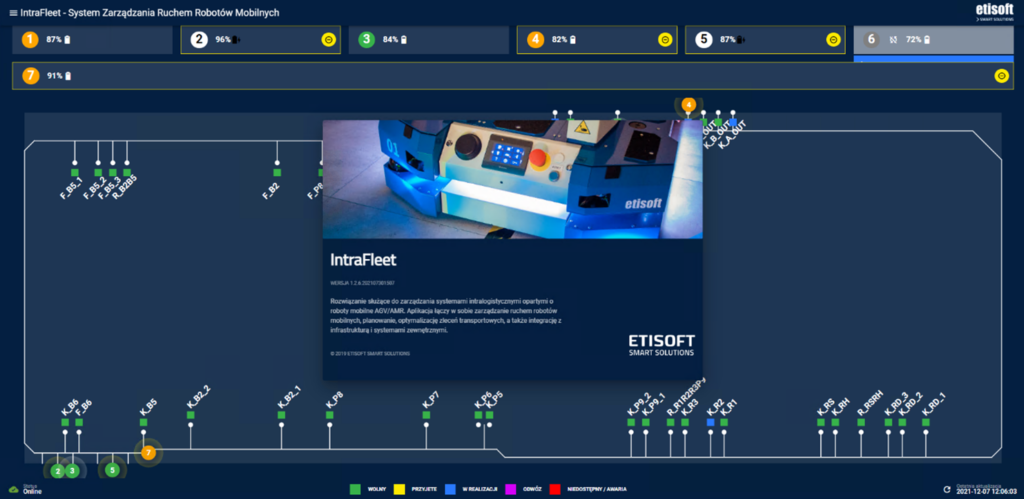
b. MES, WMS
Automatic triggering of transport missions for transport equipment is possible thanks to full integration of the customer’s IT systems, mainly the MES (Manufacturing Execution System) which is responsible for communicating and informing the production area. Automation of the intralogistics system using autonomous robots is another step towards IIoT (Industrial Internet of Things) since is requires the devices to be connected and information to be collected in real time.
Another class of the IT system is WMS (Warehouse Management Software), which is the software for managing inventory and flow of materials in the warehouse. This class of the system can be expanded by a module that makes it possible to register and prepare finished products for shipment.
Need more information about mobile robots?
In the next article we will describe other two components of the system.