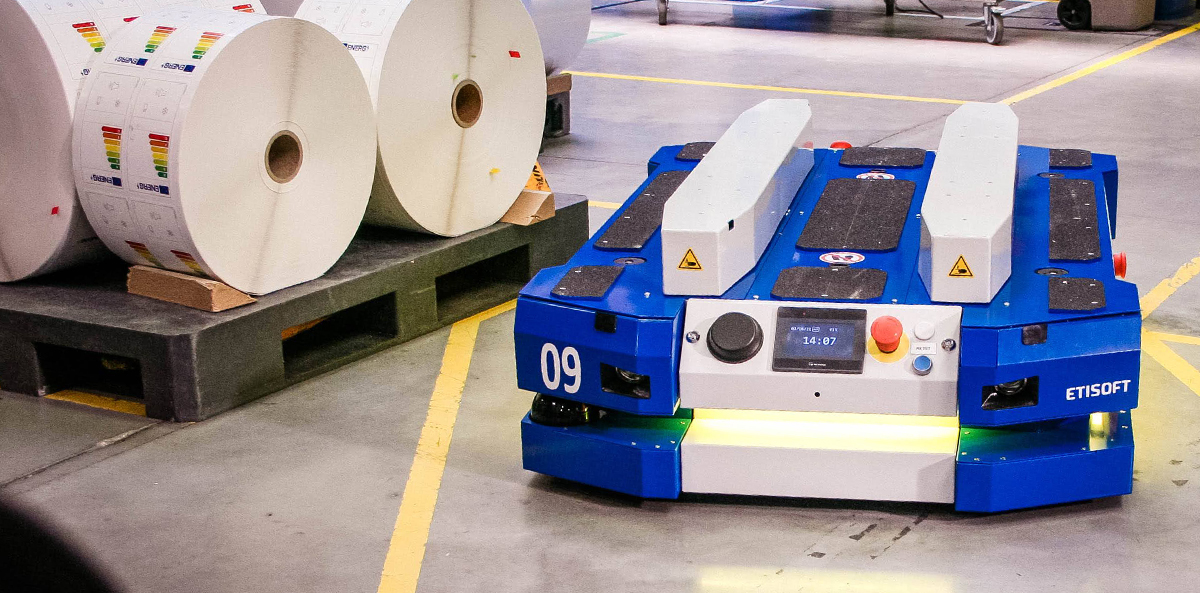
Secure deployment of AGV and AMR mobile robots with Etisoft
Mobile robots, commonly referred to as AGVs or AMRs constitute an essential element of the equipment in Industry 4.0 factories and warehouses. The arguments for their use are many. These are, among other things, ensuring work safety, efficiency and reliability of the system, a quick return on investment and alternative to the shrinking labour market. Investment in mobile vehicles, like everything new on the market, is accompanied by many questions and doubts. We want to minimise the risk, but we are also afraid of changes.
In this text we will focus, above all, on the safety, in a broad sense of the term, of investment like AGVs/AMRs. Specialists from Etisoft Smart Solutions, manufacturer and integrator of the solution, will take the role of experts answering the most common questions connected with transport robots.
AGV safety systems
Safety systems of mobile robots are undoubtedly one of the most significant aspects that should be addressed during the robot design stage as well as during deployment.
During the designing stage many possible situations and scenarios which could lead to a hazardous situation must be predicted. After a thorough risk analysis supported by the requirements of such standards as e.g., ISO 3691-4, necessary corrections and modernisations can be introduced which will constitute the safety system without forgetting about its appropriate integration with the control system. The best results are obtained if there is a close synergy between these two systems. The result is a product which is both intelligent and safe. LIDARs have already become standard equipment of AGV robots. However, for an autonomous truck to be safe for other vehicles and people, and to collaborate with the existing infrastructure, special attention must be paid to numerous parameters of the robot, e.g.,
- Surface – in case of slippery surface in the plant in comparison with a standard concrete surface an extension of the monitored obstacle detection zones may be required.
- Speed – a change of the maximum speed of the robot with the load may be required due to an unusual distribution of the transported goods.
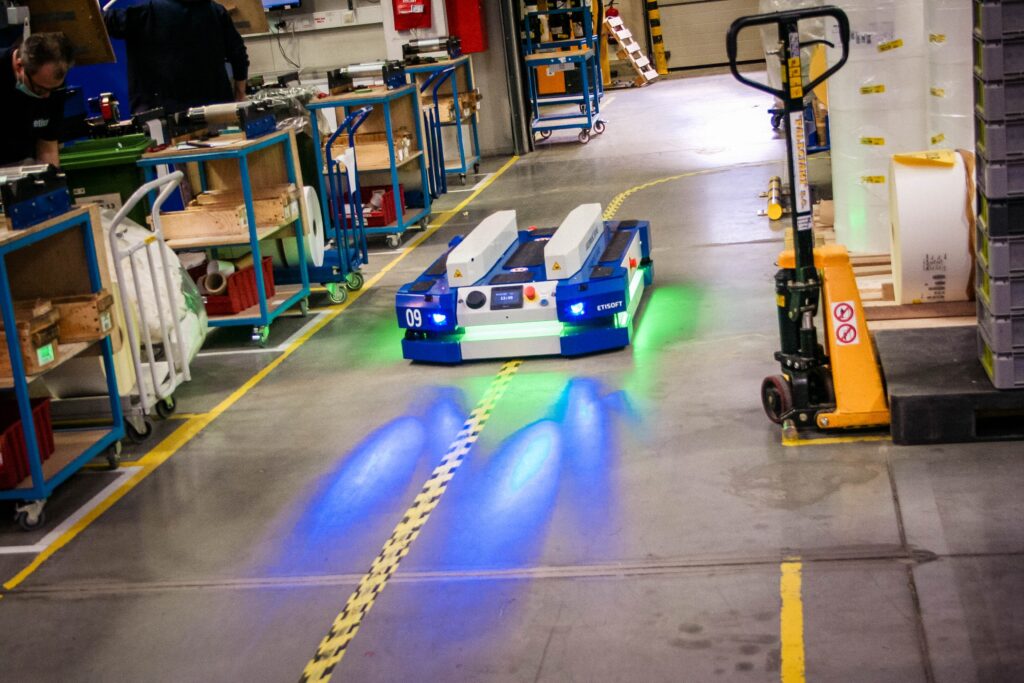
Not only the risk related to causing injury can be avoided in this way but also damage to the transported products.
Despite ensuring top quality and efficiency of safety systems, its adaptation to correct and safe operation is essential. (Dominik Ługowski, safety and control systems engineer, Etisoft Smart Solutions).
Safety through simulation of logistics processes
The design and concept stage is extremely important for the deployment of the intralogistics system based on, among other things, AGV/AMR robots. Its result is a parametric simulation of the process. It is a virtual representation of the real process that can be subject to variable production conditions during which the behaviour of individual components can be observed. Depending on the process, when building the simulation, the following things should be determined: time of the production cycle, location of logistical points, designation of communication routes and size of the mobile robot fleet. Additionally, mobile robots are also described with the use of a set of parameters such as speed of movement, loading/unloading time, battery charging time and others that result from, for example, safety requirements of mobile robots. Based on the conducted simulation, we can determine whether the required process performance indicators will be met with the assumed parameters of the mobile robot fleet.
The use of an intralogistics process simulator makes it possible to carry out many scenarios and variants of the assumed process without the need to conduct costly work at the customer’s site. This attitude also makes it possible to identify potential problems earlier and to prepare appropriate countermeasures, which will also speed up works connected with the actual integration and deployment. (Magdalena Adamczak, simulation and optimisation specialist, ESS)
Safe transport management and optimisation, i.e., process safety
The whole robot fleet and associated infrastructure are managed by the IntraFleet master system. The IntraFleet system ensures, among other things, management of the AGV battery charging process, optimal delegation and arrangement of tasks/missions, collection, and processing of information from logistical points, and monitors the operation of each vehicle, thereby ensuring continuity of delivery and logistics processes. Simultaneously, IntraFleet cooperates with the ERP and MES systems while ensuring automatic exchange of data with the Customer’s systems in real time.
Thanks to that and many other functions, the master system constantly supervises, monitors and controls operations of all the components of the automatic transport system, which guarantees process safety.
Physics simulation – already at the design stage
In the process of designing mobile robots and collaborative devices, it is good practice to use simulations. The application of dynamic simulation technology makes it possible to verify the concept of product operation without the need to produce prototypes and tests which will provide data regarding the operation of the device. This solution saves invaluable time as well as a large amount of resources, which is directly connected with cost savings. Simulations are a valuable contribution to the verification of the assumptions regarding kinematics and dynamics of the robot, and to the verification of the assumed loads the robot may experience. During simulations, among other things, collisions, impacts, loss of equilibrium, slips of robots, devices, and objects in their immediate vicinity are tested, where specific information regarding forces, velocity moments, accelerations and positions in systems is obtained.
The design, simulation and correction cycles can be repeated as frequently as needed to obtain satisfying results and a design which meets the intended requirements.
Simulations make it possible to represent the complex field of physics, that is mechanics. Another exceptionally valuable aspect is building and testing the device control algorithms during simulation prototyping, which is particularly useful in robot control development works. Thanks to that, works related to, among other things, robot navigation, control of drives, sensor signals, safety system, can be realised at the very design stage, and not only after the completion of the prototype construction. (Olaf Dudek, R&D manager)
Reliability of operation thanks to the components from renowned suppliers and transport security
Because of their industrial application, products in mobile robotics and collaborative devices must be equipped with components characterised by high reliability and durability so that they can continue to operate with the required precision for years to carry out customers’ processes. There are many technical solutions and components which can be roughly allocated to amateur, industrial, military areas and others. The components performing the same functions depending on the group are more or less unreliable, which is also frequently related to their cost and delivery time. The Etisoft Smart Solutions systems are prepared in a professional way, with the use of components of renowned brands that provide control systems, sensors, power electronics, and especially security system components.
It is thanks to the application of the top shelf components that our products can carry out the task of safe transport in a reliable manner, through such safety functions as detection of the presence of workers, obstacles, control of drive and brake systems, position, load, and state of charge of batteries.
Moreover, all positioning, navigation, detection, and orientation functions are performed by components of renowned brands, thanks to which precision and reliability do not only meet the provisions of standards and requirements but also customer expectations. (Olaf Dudek, R&D manager)
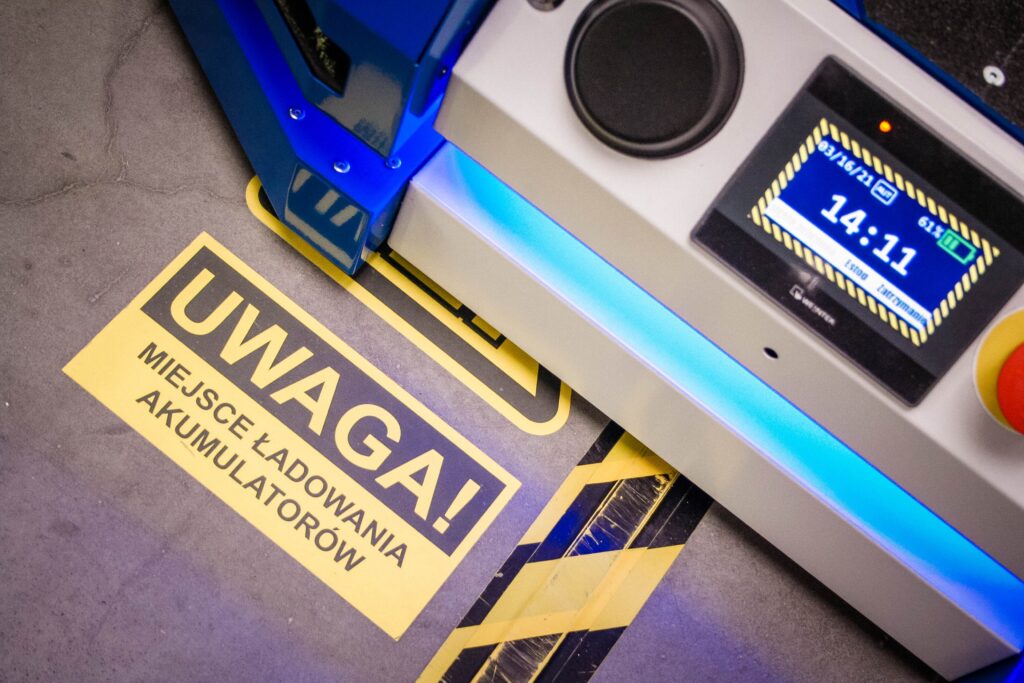
Standards guarantee safety of using mobile robots
Mobile robots and associated equipment manufactured and supplied by Etisoft Smart Solutions are machines, therefore they must meet the essential requirements of the Machinery Directive 2006/42/EC, which generally deals with production and final form of the product. There are many types and kinds of machines, whereas devices such as robots are strictly specialised solutions which are subject to standards with detailed requirements. Such standards are, among other things, standards related to machinery safety, in a broad sense of the term, for design principles, risk reduction, prevention of collisions with humans, electrical systems and control systems. The most significant standard among the requirements for autonomous vehicles is the PN-EN 3691-4 standard which entered into force last year and replaced the old PN-EN 1525 standard of 1999. This standard differs significantly in terms of requirements, if only due to a different perception of technological progress more than 20 years ago. The above-mentioned safety standard and the EMC Directive are fully observed for our products, which makes it possible to deploy fully safe and functioning systems at our customers. (Olaf Dudek, R&D manager).
Security of investment
The position, recognition, and reliability of Etisoft, a company that is successfully operating on international markets, stand behind the solutions offered by Etisoft Smart Solutions. Etisoft, which has existed for almost 30 years, is a technologically mature company on the market of manufacturers and suppliers of functional components for many industries. The strength of the brand is its stable position and consistent work on the development of the company that comprehensively supports production automation. Therefore, a decision was made to expand the portfolio and support customers interested in automating their processes through, among other things, AGV/AMR mobile robots.
Feel free to contact us: