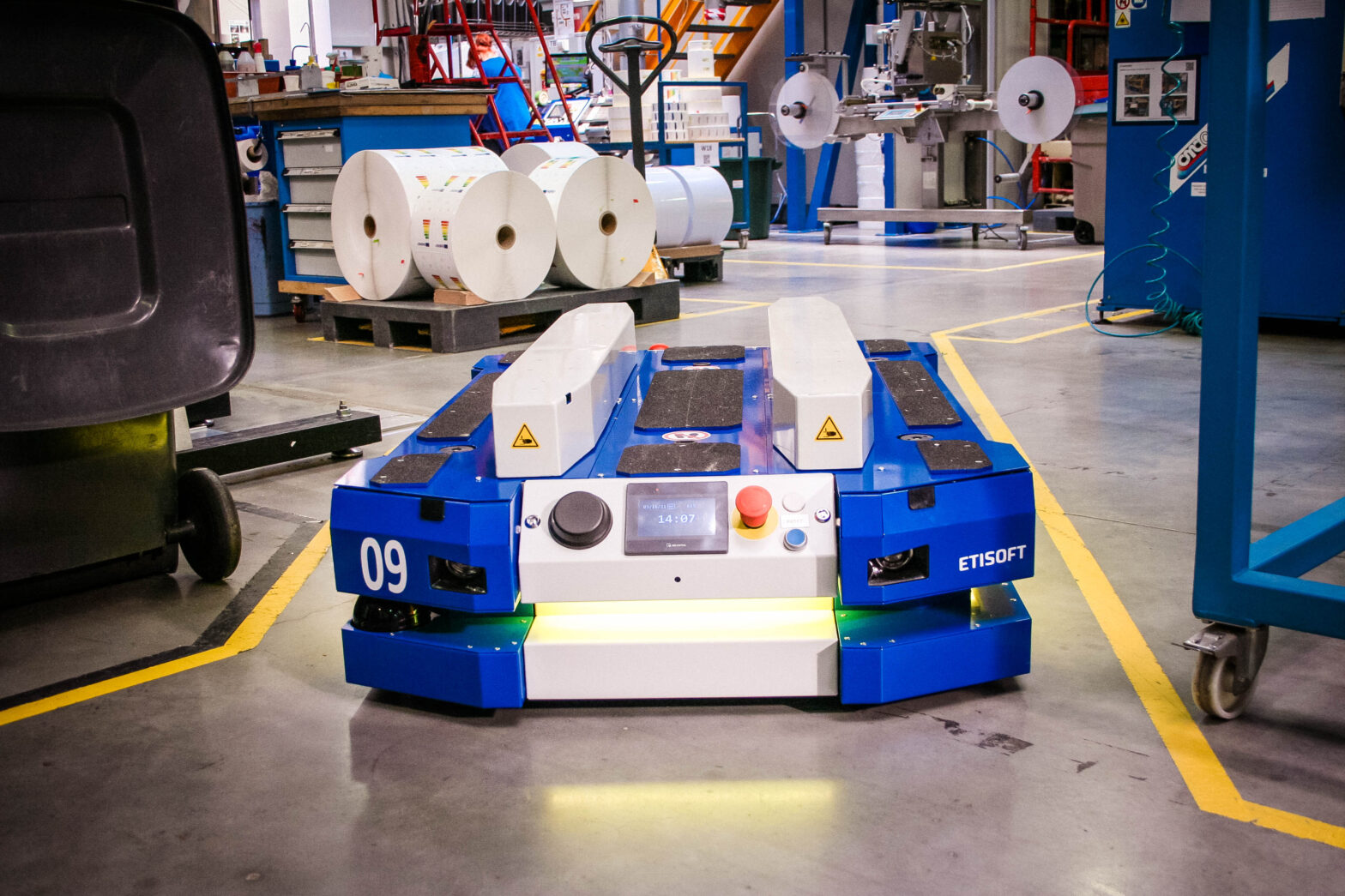
Implementation of an intralogistics system with the use of an AGV robot at the label production plant Etisoft Sp. z.o.o
The implementation of the intralogistics system took place at the Etisoft company at the turn of 2020/2021. We have designed, integrated and implemented a complete intralogistics system based on an AGV robot.
Etisoft is a leader in its industry. The solution that has been implemented shows the possibilities of automating logistics processes, even in production plants and warehouses with limited space and busy transport paths.
AGV robot: optimization and automation of logistics processes
The aim of the project was to optimize and automate logistics processes in such a way as to relieve employees of the internal logistics department during time-consuming and repetitive activities on three production shifts. During the implementation of the project, a big challenge that our engineers had to face was the small amount of space between production stations and crowded transport paths. The implementation of the system included
- an AGV robot,
- storage docks,
- a screen showing the location of the robot and its operating parameters,
- a system for informing about the status of the docks using “andon” signaling devices and,
- the IntraFleet system – managing the robot’s work, transport orders, integrated with the MES system for production management.
In addition, thanks to the implementation of the system for a Group company, our clients have the opportunity to carry out reference visits and find out about the possibilities of intralogistics systems and the advantages of the proprietary solution of the daughter company Etisoft Smart Solutions Sp. z.o.o.
Operation of the plant before automation
Before the project was implemented, the warehouse staff operated the flexographic machine stands with the use of hand pallet trucks and pushed table trolleys. The scope of responsibilities of the logistic employees was also to deliver empty pallets to the above-mentioned positions.
The functioning of the enterprise after automation
The transported logistic unit is a standardized EPAL pallet. A standard load placed on a pallet consists of several to a dozen rolls of labels produced by the customer with a total weight of up to 500 kg. Machine operators, after filling the pallet or completing the order with the help of the operator panel, trigger a transport request, as a consequence of which a transport mission for the AGV robot is generated to the appropriate destination logistics point based on data from the production management system. After the pallet has been transported with the load, an empty pallet is delivered to the station for the next order.
Infrastructure
In the designed automated transport system, the engineers used the IntraBot Lift 550 robot, whose lifting capacity is 550 kg, and its design allows for rotation on the spot, which is of great importance when entering the docks. In order to enable picking up and putting away pallets from logistic points, 6 storage docks were installed. A synoptic board has been installed in the hall showing the location of the AGV robot. The target docks have been equipped with light signals informing the employees of the warehouse department about the need to pick up the pallet from the dock.
Intralogistics system capabilities adapted to the client’s needs
Although the mobile robots manufactured by Etisoft Smart Solutions Sp. z o.o. allow for autonomous driving (AMR), in order to increase the reliability and precision of driving, for the needs of this plant the robot moves along dedicated paths on mounted magnetic tapes (AGV), increasing the safety of employees who can predict the path of the vehicle’s movement. An additional benefit of implementing the system is the improvement of order within the transport paths.
The second aspect of safety was limiting the robot’s speed depending on the zone. Although the robot can reach a speed of 5 km / h, in order to ensure full safety for employees in the hall, it moves at a speed of up to 2 km / h. It slows down to 1 km / h when there are people or objects within the warning zone, and stops when the protection zone is violated. Everything serves to maintain the safety of employees and the safety of the cargo being transported.
There are people behind the success of the implementation
The implemented intralogistics system proves the possibility of processes automation in the existing halls with full safety for people and loads. However, it should be borne in mind that an important factor influencing the success of the project in this case was and still is the discipline of employees, openness to innovation and commitment of the management.