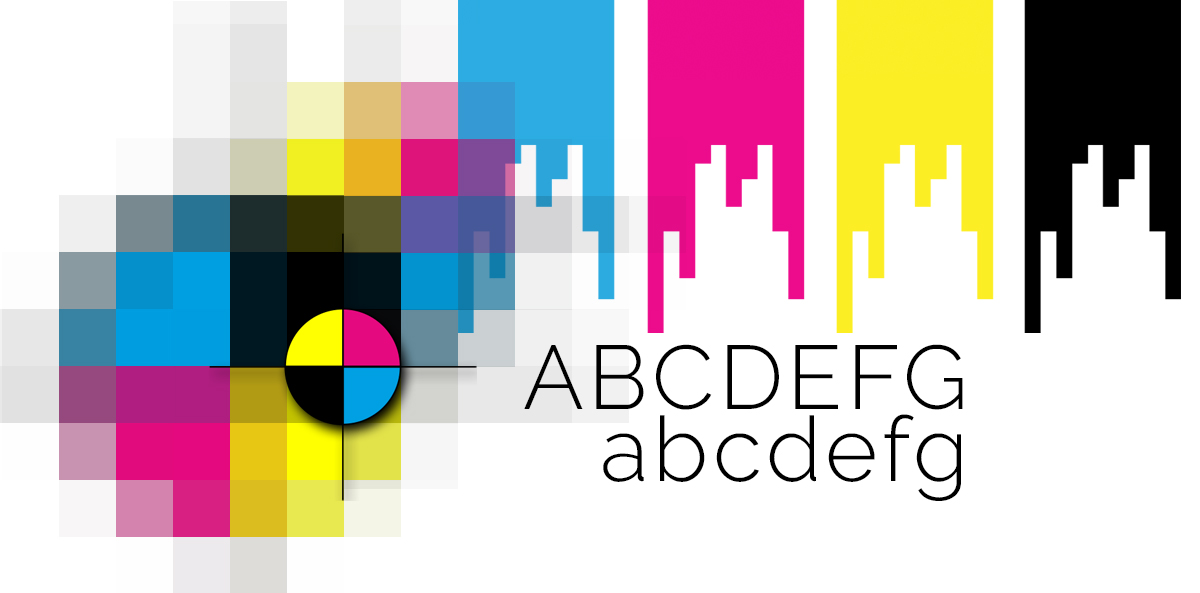
Digital printing
Digital printing is nowadays one of the most popular and continuously developed printing methods in the world. Today, almost every print shop has digital printing machines. Several years ago, digital presses were only a supplement to the traditional equipment in print shops, however, this situation has changed together with technological development. In recent years, the printing market has been dominated by digital printing, and the world’s largest companies have been competing with one another by introducing newer and newer technologies. Customer requirements have also changed, and the so-called print-on-demand has begun to reign. Nowadays, the most frequently ordered products are low-volume or even one-off runs with high-quality prints, and customers expect their orders to be completed at an express pace. In such cases, technologies such as digital printing work perfectly.
Digital printing – what does it mean?
For people outside the printing industry, the notion ‘digital printing’ is a meaningless slogan, although each of them comes across digitally printed products on an almost daily basis. Most people are not able to distinguish traditional printing techniques, let alone tell the difference between prints made using digital technologies.
So, what does digital printing mean? Briefly, it is a set of various printing technologies which have in common absence of any matrices, stencils, photopolymers, or other permanent moulds with an image applied and used to reproduce it. We can distinguish a few main and most frequently used methods of digital printing. These include electrophotography, thermography, sublimation, and ink-jet printing.
Regardless of the selected digital printing technology, the image recorded in the form of a digital file is appropriately processed in the printing machine and sent to the print heads in the form of a digital signal. This takes place each time, with each subsequent printed copy. This allows you to enter variable data into the print, i.e., the so-called personalisation. This means that each subsequent copy, each subsequent product coming out of the machine can have a different print differing from the previous one by small detail or a different image.
Digital printing technologies and their applications
For people outside the printing industry, the notion ‘digital printing’ is a meaningless slogan, although each of them comes across digitally printed products on an almost daily basis. Most people are not able to distinguish traditional printing techniques, let alone tell the difference between prints made using digital technologies.
So, what does digital printing mean? Briefly, it is a set of various printing technologies which have in common absence of any matrices, stencils, photopolymers, or other permanent moulds with an image applied and used to reproduce it. We can distinguish a few main and most frequently used methods of digital printing. These include electrophotography, thermography, sublimation, and ink-jet printing.
Regardless of the selected digital printing technology, the image recorded in the form of a digital file is appropriately processed in the printing machine and sent to the print heads in the form of a digital signal. This takes place each time, with each subsequent printed copy. This allows you to enter variable data into the print, i.e., the so-called personalisation. This means that each subsequent copy, each subsequent product coming out of the machine can have a different print differing from the previous one by small detail or a different image.
Digital printing technologies and their applications
Electrophotography, i.e., laser printing
The oldest, but continuously developed, digital printing technology is electrophotography which originated from the well-known xerography. In the 1990s, the first laser printers using electrophotographic technology were launched and are still used today. The image there is created in them by laser irradiation of a rotating cylinder (the so-called photoreceptor) which is covered with a special coating. The exposed areas attract a colour powder called ‘toner’ thanks to electrostatics. The toner is drawn onto a sheet of paper or another substrate with electrodes, and then, fused and fixed to the substrate through exposure to high temperature.
This technology has been continually improved over the years. Over time, printers were developed not only for office and home use but also for high-volume sheet-fed and continuous printing (roll printing). Thanks to the high quality of laser printing print shops use these machines as an alternative to offset technology for printing low volumes of advertising materials, catalogues, leaflets, personalised and numbered prints, photo albums as well as low-volume books, brochures, and instructions for use.
The machines are also used in banks and institutions for transactional printing, printing personalised documents sent to clients, for bulk printing of bills and invoices, etc.
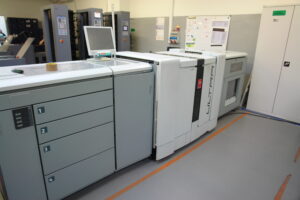
Ink-jet printing
It is the most common and cost-effective method of digital printing. We all know it from simple inkjet office printers. Not everyone knows though that this method has a much wider scope of applications and is used on an industrial scale in many branches.
A print head or a set of several print heads that print together is at the heart of each ink-jet machine. Each head has hundreds of microscopically small nozzles, which precisely eject droplets of colour liquid which contains dye. Due to the types of these liquids, which are commonly called inks, several varieties of ink-jet printing can be distinguished.
Pigment printing – it is a type of inkjet printing used in simple printers, but it is characterised by much better durability and resistance to contact with water. It is used for very fast industrial reel printing, mainly on offset paper. This technology has been recently used in large press printing houses and print shops specialising in book printing. Thanks to its speed and no need to make expensive moulds, the technology is winning the publishing market and replacing traditional offset printing equipment.
Solvent, mild solvent and eco-solvent printing – this type of printing uses inks made from solvents like those used in varnishes which after evaporation leave a mixture of resins and dye on the substrate. Such prints are characterised by exceptionally high durability, resistance to sunlight and weather conditions. This method is commonly used in large format plotters for low-volume printing of all kinds of posters, advertising media, banners, billboards, etc.
Latex printing – printing technology which uses a special odourless ink being a colloidal mixture of synthetic resin coloured with coloured pigment, water, and organic solvent. The print is fixed through exposure to high temperature, thanks to which it is already dry and ready for further processes after leaving the machine. The print is characterised by exceptionally high durability similar to that of solvent printing. Nevertheless, due to the absence of odour and toxic components, it can also be used for printing e.g., wallpaper, fabrics or other materials which are placed indoors.
UV printing – inkjet printing technology using inks fixed with UV radiation of a specific wavelength. Because of exceptionally high print durability and excellent adhesion to almost any substrate it is mainly used in large format plotters for printing all kinds of advertising and information boards, road signs, rigid plastic sheets, composites, metal sheets, wood and glass.
For years, this technology has also been used for reel printing in the label industry where it successfully competes with flexographic printing. This makes it possible to quickly produce multi-coloured labels or other products without incurring the cost of making polymeric matrices or other kinds of moulds.
Digital UV printing is also more frequently used for low volume or even single item printing. Special UV plotters have been designed for this purpose, in which we can place small objects, advertising gadgets, lighters, pens, CDs/DVDs, appliance cases and all and any other objects which require printing.
Sublimation printing – is also a technology that uses digital inkjet printing. It is the so-called indirect technology as the print is made on special transfer paper using plotters or printers and proper inks. The printed paper is placed in a special thermal transfer press which presses it to the substrate. The phenomenon of sublimation, i.e., the direct transition from the solid to the gaseous state bypassing the liquid state, occurs at high temperatures. Under simultaneous pressure and high temperature, the colour particles evaporate from the transfer paper and as a gas penetrate into the substrate binding permanently with it. This technology is used, for example, for marking objects, applying colour print to advertising gadgets, mugs, clothes, T-shirts, caps, umbrellas, lanyards, etc. The technology is used on the largest scale in the clothing and textile industry. It is used on an industrial scale for transferring the print to fabrics in rolls as well as to finished clothing products.
DTG printing – the name comes from an English term ‘Direct To Garment.’ It is a technology which uses digital inkjet printing to directly apply a colour image to objects and textiles. It has gained its popularity due to the low price of equipment and low operating costs thanks to which it successfully replaces screen printing and pad printing. Unfortunately, due to a relatively slow print speed, these devices are mainly used for low-volume or one-off printing. They are often used by small print shops and advertising agencies for small orders.
Besides commonly used laser and inkjet printers or office “combos,” at every step we can come across all types of printing devices using various digital technologies. Examples include thermal or thermal transfer printing.
Thermal printing – is a technology commonly used in all types of cash registers, scales, or fiscal printers. The print is conducted on special paper which blackens under the influence of heat delivered to the print head. The advantage of this technology is the print speed and the fact that the only consumable is the paper itself, and no inks, paints or ribbons are necessary. Unfortunately, the prints are very nondurable, and they become illegible over time.
Thermal transfer printing – the pigment from the colour ribbon is transferred to the paper because of point heating and pressing to the substrate. This technology has found widespread application in various types of small label printers, scales etc., and is used, above all, for marking goods, printing personalised labels, barcode stickers, etc.
Nowadays, digital printing machines are the most dynamically developing segment in the entire printing industry. They are the answer to changing market needs and end customer expectations. Nowadays, everyone avoids ordering stock to reduce high storage costs and minimise the risk of outdating of products. It is due to this fact that digital technologies have become so popular, providing the possibility to print on demand any quantity of a product without incurring the costs of making print moulds and the costs of changeover and start-up of traditional machines.
However, this does not mean the end of traditional printing methods. Offset, flexographic, and screen-printing technologies are and will still be used wherever medium to large runs are required. It is related to the fact that the costs of print moulds and launching of production are distributed over the whole print run. In addition to that, traditional printing techniques, contrary to digital ones, make it possible to use inks with special properties, custom mixed colours, metallic inks, pearl inks, luminescent inks, etc.
In the coming years, this trend is certainly not going to change, and we will see further intensive development of technology and digital devices themselves.
Interested? Contact us.