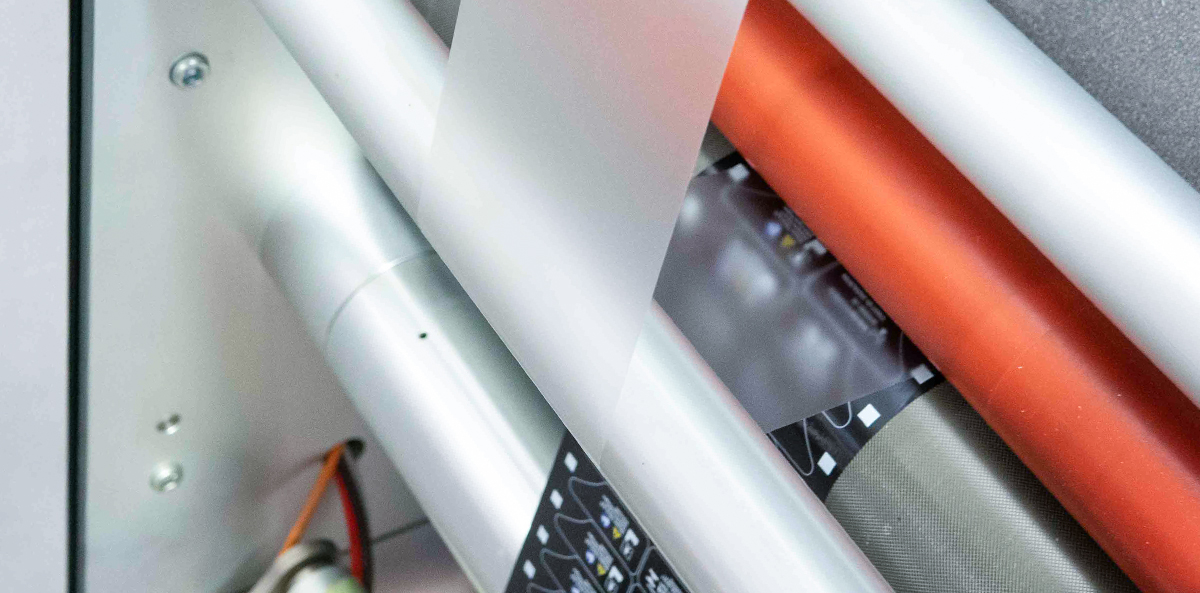
Can lacquering and lamination of labels guarantee label durability?
Self-adhesive labels function in very different conditions. They are frequently exposed to heavy soiling, mechanical friction, aggressive substances, weather conditions, and radiation. That is why, when selecting a labelling solution, it is so essential to ask the customer the basic questions about the durability of the application, and what conditions the label and its print must withstand. Questions about how to effectively secure the print boil down to:
- will the label be exposed to any damage and external factors?
- what will the label be applied to?
- how long should it remain on the product, in other words, how durable must the label be?
If we know that the label will “function in harsh conditions,” then its print should definitely be durable and resistant to external factors.
So, how can we secure labels?
When manufacturing printed labels using a flexographic or a digital method, to increase their resistance it is often required to additionally secure the print. Two methods are most commonly used:
- lacquering
- lamination
What does label lacquering consist in?
Label lacquering consists in covering the entire surface of the label or its part with an additional, transparent layer of varnish. An additional layer of varnish (glossy or matte) improves the aesthetics and secures the print against friction and smearing in direct contact with water and other more aggressive liquids. Lacquering is possible only during label manufacturing before the cutting process.
What does lamination of self-adhesive labels consist in?
Lamination consists in attaching an additional transparent film to the whole surface of the label to be secured. Through lamination we obtain labels with high durability. The laminate provides total resistance to smudging and abrasion of the print, and significantly increases the mechanical durability of the label. Appropriately selected laminate undoubtedly provides resistance of the print and the label to the majority of chemical substances (oils, greases, petrol, brake fluid, alcohol, toluene).
Advantages of using a laminate:
- proper laminate increases label aesthetics:
– laminate with glossy surface increases contrast and depth of colour
– laminate with matte surface decreases the above.
- properly selected laminate improves physical and mechanical parameters The laminate increases the label thickness, which is strictly specified in some applications. In the case of automatic application, the use of a laminate increases the stiffness of the structure, which makes it easier to peel off the backing
- Laminate can also be a temporary protective film. In case of some applications, it is necessary to mark the product before the painting process. Such processes certainly make it impossible to read the information on the label. In such cases, the laminate can be used a temporary form of protection. The laminate should have an appropriate adhesive and the structure of the label must ensure that the label can be peeled off without damaging the actual printed label.
When to use labels secured with a laminate?
Examples of applications where the lamination is broadly used:
- for permanent marking of goods intended to be used for many years (e.g., rating plates)
- for identification of model and serial numbers of devices – identification labels
- for safety warnings and recommendations, e.g., warning labels
- inventory labels
- laminate as a temporary surface protection film.
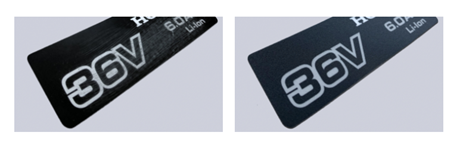
The most popular types of laminates:
- polypropylene film – quite stiff, with high mechanical resistance and limited resistance to increased temperature
- polyester film – the most frequently used material for label lamination – characterised by good mechanical resistance, remarkably high resistance to chemicals and temperature. It is suitable for outdoor use
- polycarbonate film – characterised by the highest mechanical resistance.
The 3M Polycarbonate film is an interesting solution in this area.
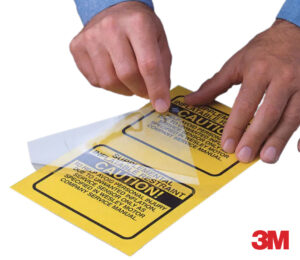
It gives the label a “technical” look while significantly increasing its aesthetic value. In spite of its matte finish, it makes the colours clearer and more intense.
High mechanical resistance and resistance to many chemicals, including Isopropanol and some fluids used in the automotive industry. The range of temperature from -40oC to 121oC. Summing up, the choice of the appropriate laminate depends on the conditions in which the label will function and what factors it will be exposed to. In this matter, customers can fully depend on the assistance and advice of our technologists.
If you have any questions, do not hesitate to contact us!