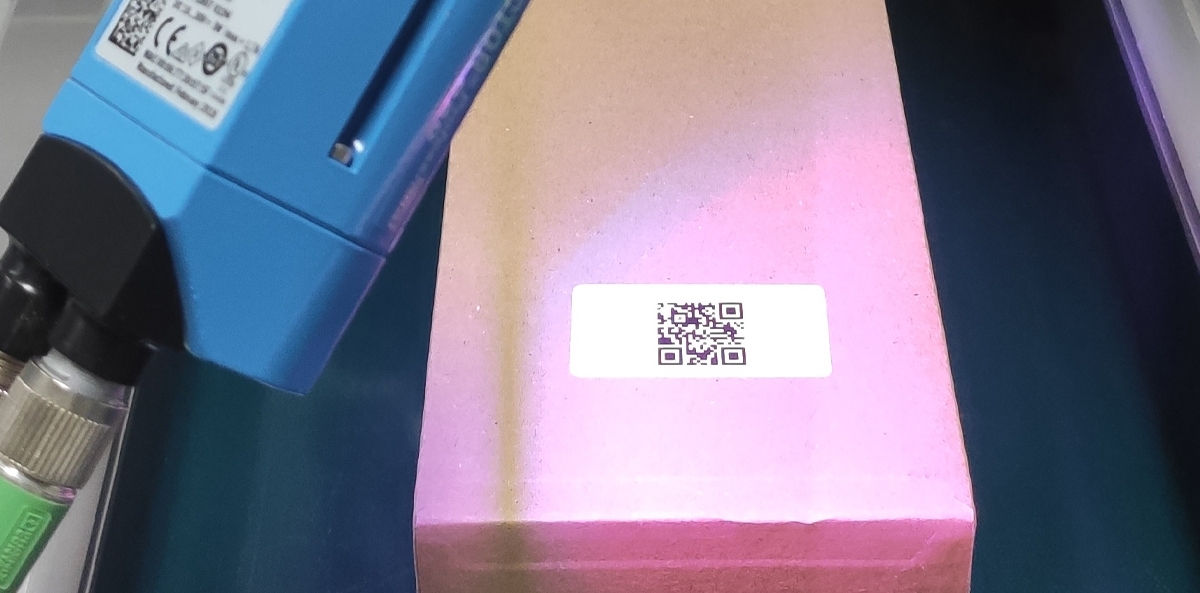
Automatic labelling. How and when verify the correctness of a label applied in this way
Automatic label application makes it possible to easily facilitate the product labelling process. The advantage of automatic labelling is that the place of label application is repetitive, taking into consideration a certain tolerance, and that the data on the label are correct.
However, it may happen that in some situations the product is not labelled (no label), the labelling is incorrect (incorrect/illegible data on the label), or it does not comply with the assumed quality criteria.
Automatic labelling and situations requiring attention
Adverse events can occur in the event of:
- Failure of the applicator or thermal transfer printer
- Manufacturing defects or wrong selection of consumables
- Damaged thermal transfer printer head
- Lack of media supplying the label applicator, such as electricity, compressed air
- Lack of communication with the system generating labels for printing
- Incorrect labels inserted into the applicator or incorrect data submitted for printing
- Incorrect application of labels to products (shifts, folds, wrinkles).
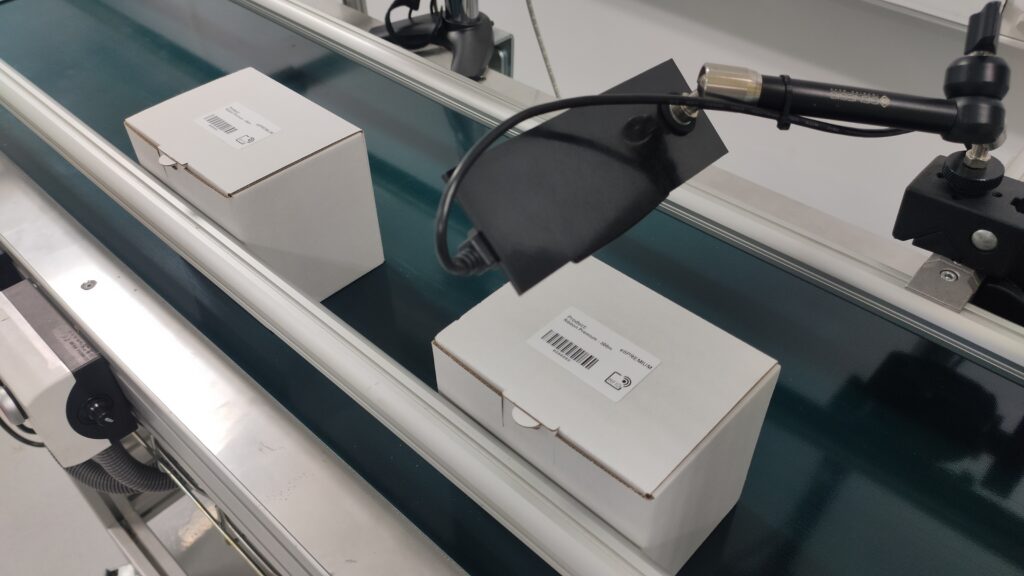
How to verify the presence of the label on the product after its automatic application?
- Verification with a bar code or 2D code scanner
A bar code or 2D code is frequently the most significant information on the label. It can contain identification data required for, e.g., scanning the product at the shop counter or at subsequent stages of the assembly process, or other information such as, for example, website addresses. Using the scanner, we can easily and cheaply determine whether the applied label with a code is on the product. If the code cannot be read by the scanner, it means that the label was not applied or the 1D/2D code is damaged. This may happen, e.g., if the TT printer print head is damaged or the thermal transfer ribbon is wrinkled, the consumables are wrong, the printing temperature is too low, etc.
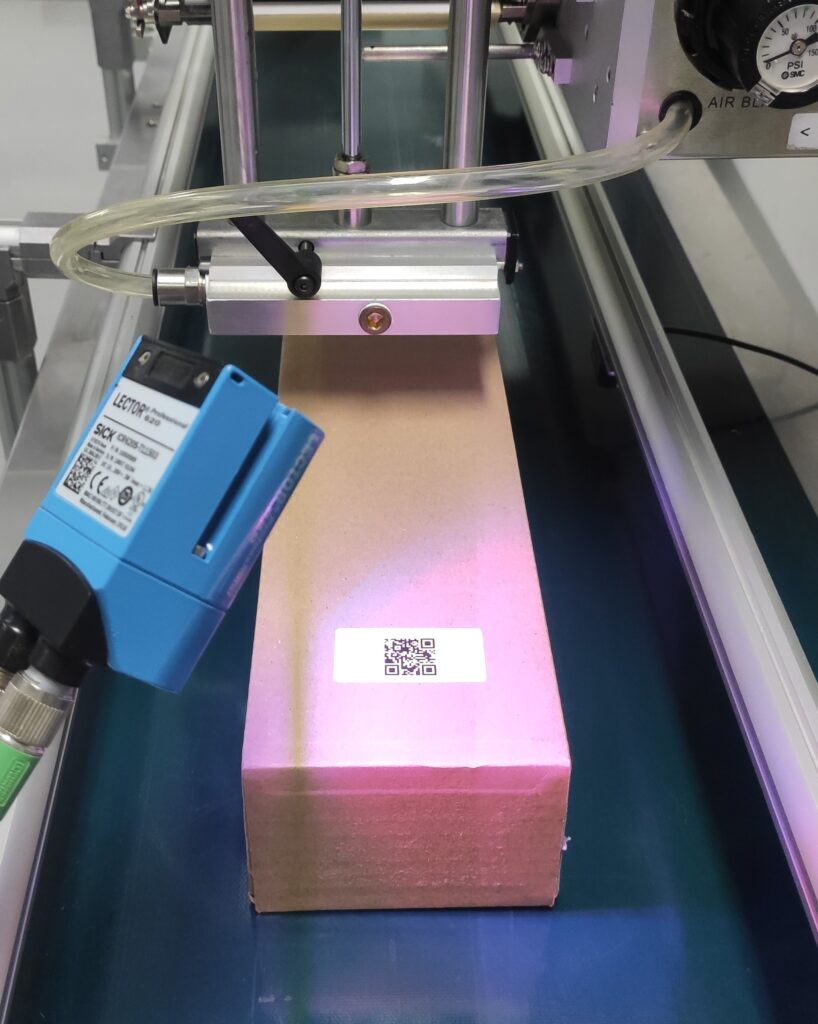
- Verification with contrast and colour sensor
We can also easily and cost-effectively check the presence of the label on the product using a contrast or colour sensor. Such a sensor can detect the presence of a label on the product when the differences between the colour of the label and the colour of the surface to which it is applied are not similar. Such verification will help to determine whether the label was applied and whether the place of application is correct.
- Verification using the vision system and OCR scanners
If it is necessary to perform a very thorough verification of labels in order to check the correctness of inscriptions and pictograms, it will be crucial to use a vision system for verification. This can also be an OCR vision scanner with character decoding function.
The vision system will also make it possible to verify, with the highest accuracy, the precision of the label application to the product or workpiece, effectively supporting the process of labelling in demanding applications.
- Verification of RFID tags
Verification of the application of the label with an RFID tag is conducted using an antenna connected or integrated with the controller. Besides the presence of the RFID tag on the product, we can also verify the data stored in it and possibly conduct a validation with the information stored in an external database.
Automated labelling and the correctness of label application
How and at what stage to do it. How to check its presence on the product after automatic application? There are a few ways to do this.
It is recommended that verification of the presence of the label on the product takes place as soon as possible after the application. This makes it possible to quickly remove the product from the process or re-label it. Postponing verification may result in the multiplication of products without the right labelling, e.g., due to print head failure or failure to detect the end of the label roll. Consequently, there will be disruption to the production flow, longer downtime or even loss of products, let alone complaints from end customers.
In particular cases, if technically possible, additional verification of the label on the applicator before its application can be introduced. The preventive measure will allow for even faster verification of the data on the label and detection of inaccuracies before the label is applied. This operating procedure is desirable when we do not want an incorrectly labelled product to end up on the production line due to the lack of possibility or difficulty of locating or removing it. It should be noted that in the case of 1-to-1 labelling, i.e., with currently dedicated printed data on the label, pre-labelling verification may be hindered or impossible due to the design of the application head. The same concerns the issue of automatic removal of the already printed label from the applicator to free up space for the next printed label.
The process of verifying the label or its content after the automatic application process is a justified supplement to the automation of the production line. It provides the comfort of ensuring the correctness of labelling frequently resulting from human error despite the use of automatic labelling machines. Verification will also make it possible to better diagnose wear and tear of consumables of applicators and TT print modules or defects in the manufacturing process (e.g., dirty, wet, or greasy product surfaces causing poor adhesion of the applied labels).
If automatic labelling may prove itself useful in your company, and if you expect correctness and safety of labelling, contact us. We will help you choose the right solution!