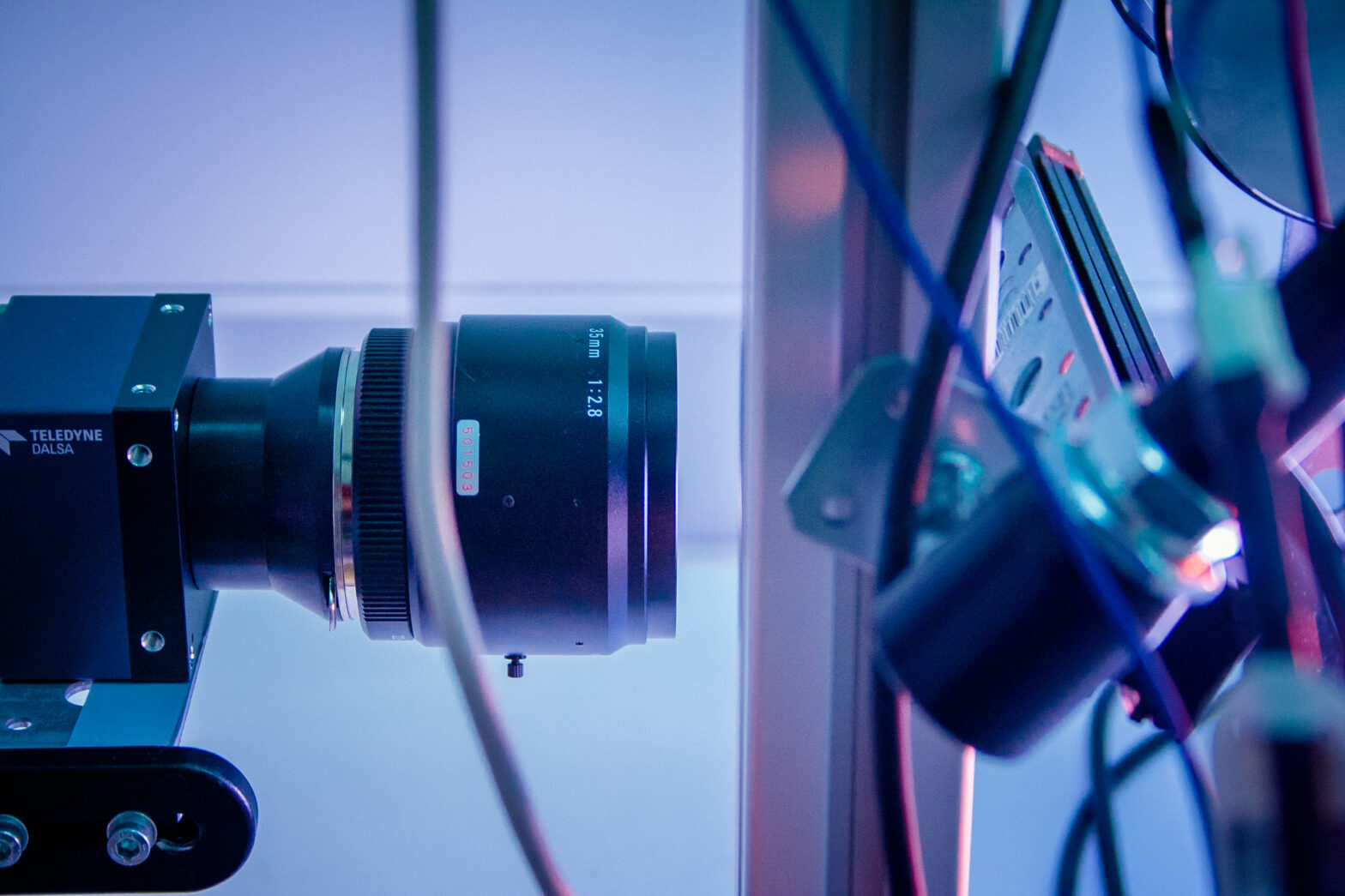
Automated quality control with the aid of a vision system in 6 steps – part 2
After reading the first part of the article you already know what the automated quality control looks like in the context of the analysis of customer needs and what business steps should be taken.
After the stage of arrangements, that is specifying with the customer the objectives the vision system for quality control is supposed to achieve, collecting information on the production process which it will be a part of, determining the feasibility of the suggested concept in the PoC stage, analyzing the business rationale of the whole undertaking and signing the contract, the time for project implementation comes. That is, the design stage, the executive stage as well as system implementation along with its testing, learning and adjustment.
Automated quality control – time for project implementation
Vision systems for production quality control created at Etisoft Smart Solutions perform advanced verification, control, and inspection processes. They can be integrated with both automation systems, such as PLCs, basing systems, or case packers, where they can control the robot’s operation, and customer IT systems. Thanks to such an approach they can operate virtually unattended and provide plenty of valuable data.
Due to advanced solutions used in visions systems, skilled mechanics, automation engineers, IT specialists and vision system specialists are required to create them. Therefore, the basis for creating an optimal vision system for production quality control is to gather a good project team. And then to determine a detailed project schedule and budget.
After drawing up the mechanical designs and circuit diagrams and based on the 3D model previously approved by the customer and considering the dimensions to adapt the system to the existing infrastructure, the workstation itself is built.
At this stage, internal tests are conducted using samples, i.e., product designs provided by the customer for the purpose of machine learning for the vision system. Before the system is assembled on the customer’s premises, final tests and pre-production start-up of the workstation are conducted. After successful testing, the system can be implemented in the customer’s factory.
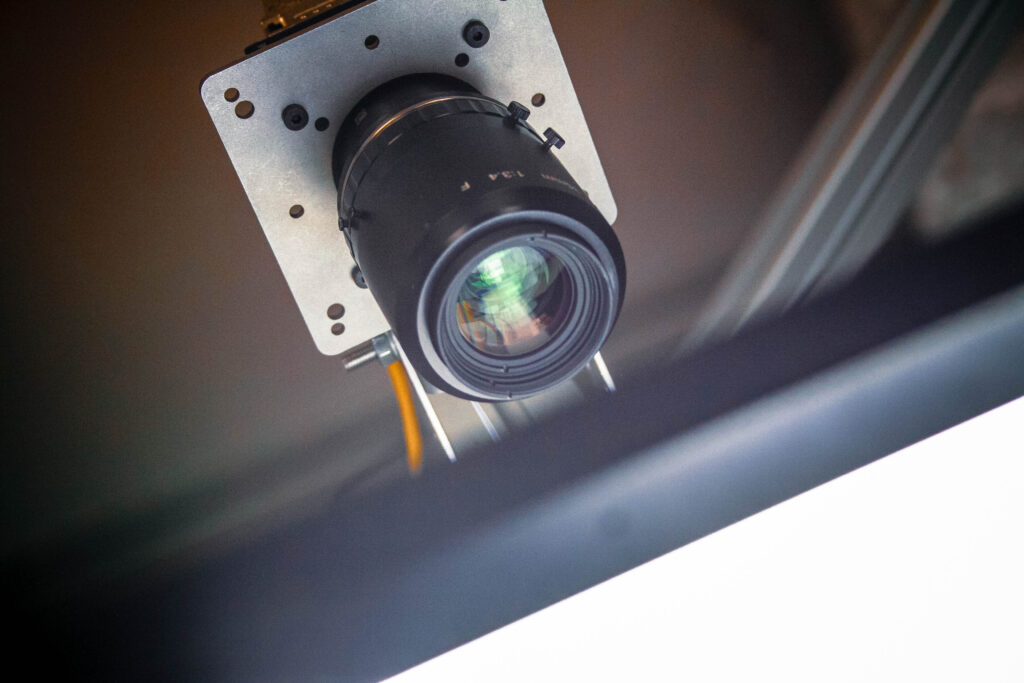
Implementation
The installation of a vision system at a customer’s facility and its integration with the production line can take from a few hours to a few days. However, this does not disrupt the production process itself.
During this time, system calibration and adaptation of the vision system to the actual conditions on the customer’s production line are conducted. Along with the system, the customer receives the instruction for use and machine documentation, whereas their employees are thoroughly trained.
The implementation ends with the final SAT/FAT acceptance of the system by the customer.
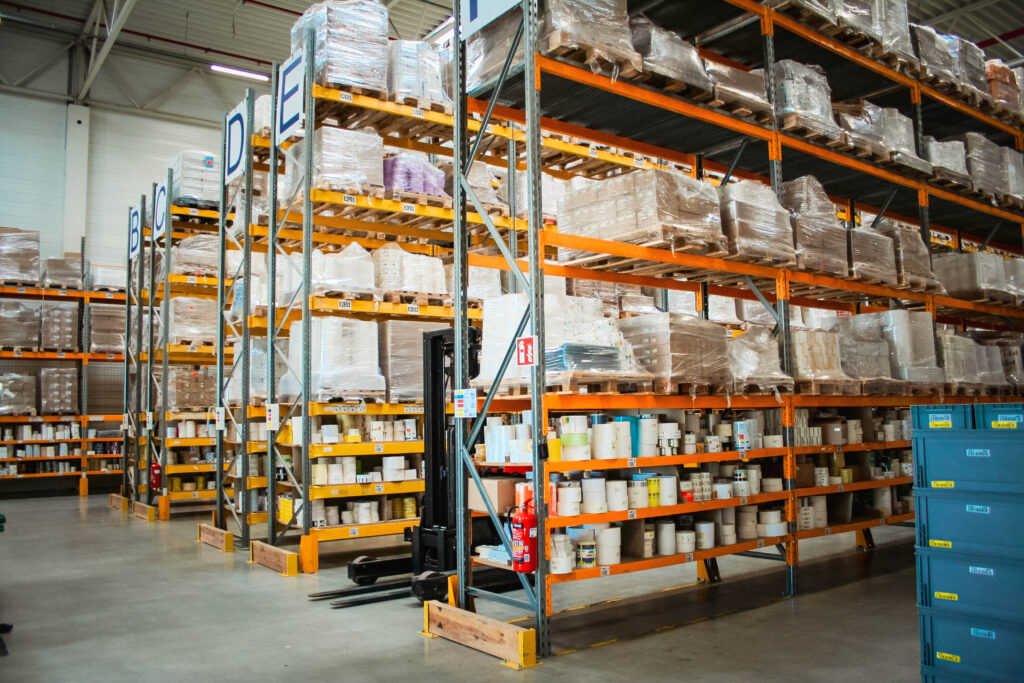
Maintenance
Vision control systems cooperating with the production line, industrial automation and MES systems constitute a basic element of the quality management process. For this reason, in addition to safety at each implementation stage, safety of use resulting from the application of high-class systems, compliance with standards and certification principles, we provide continuous supervision of the operation of the implemented system by experienced engineers, phone support and efficient warrant repairs.
And more…
The modular structure of the system and its open architecture allow for upgrades if new product variants appear. Integration with the IT systems make it possible:
- for the system operation to be conducted in an unattended way, as all data necessary for quality control can be automatically downloaded from the customer’s systems,
- to pass information on the production process in real time, which makes it possible to react in the case of any problems and, for instance, save resources, in no time,
- to conduct ongoing verification of compliance of product parameters with the specification,
- to count manufactured products and transfer this information in real time to the supply systems and warehouse,
- to trace products (traceability),
- to collect statistical data that can serve as the basis for analyses allowing changes to be made to the production process. This makes it possible not only to offer high-quality products, but also to identify areas of the process that need to be improved.
We also help you to obtain a certificate issued by the Office of Technical Inspection (Urząd Dozoru Technicznego) for our workstations.
Interested? Click below!